Как да проектираме пластмасови части
Кратко описание:
Да се дизайн на пластмасови частие да се определи формата, размерът и прецизността на частите, въз основа на ролята, която частите играят в продукта, и правилото на процеса на формоване на пластмасата. Крайната продукция са чертежи за производство на калъп и пластмасова част.
Производството на продукти започва с дизайн. Дизайнът на пластмасовите части пряко определя реализацията на вътрешната структура, себестойността и функцията на продукта, а също така определя следващата стъпка на производство на калъпи, разходите и цикъла, както и процеса и разходите за шприцоване и последваща обработка.
Пластмасовите части се използват широко в различни продукти, съоръжения и живота на хората в съвременното общество. Пластмасовите части изискват различни форми и функции. Те използват пластмасови материали и техните свойства са различни. В същото време има много начини за производство на пластмасови части в индустрията. Така че проектирането на пластмасови части не е проста работа.
Различен дизайн на части и материал се произвежда различна обработка. Обработката за формоване на пластмаса включва основно по-долу:
1. инжекционно формоване
2. издуване на формоване
3. компресионно формоване
4. ротационно формоване
5. термоформоване
6. екструзия
7. изработка
8. разпенване
Съществуват множество начини за масовото им производство. Инжекционното формоване е популярен производствен метод, тъй като инжекционно формованите 50% ~ 60% пластмасови части се произвеждат чрез инжекционно формоване, това е високоскоростна производствена способност.
Витрина за някои пластмасови части, които проектирахме:
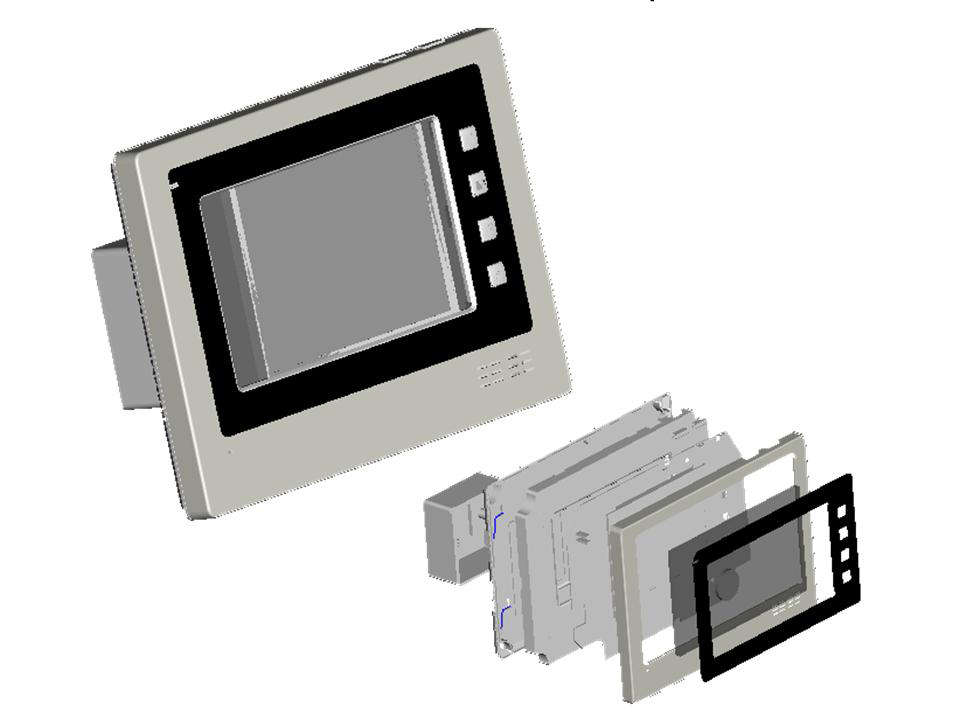
Пластмасова кутия за телефон за зрение
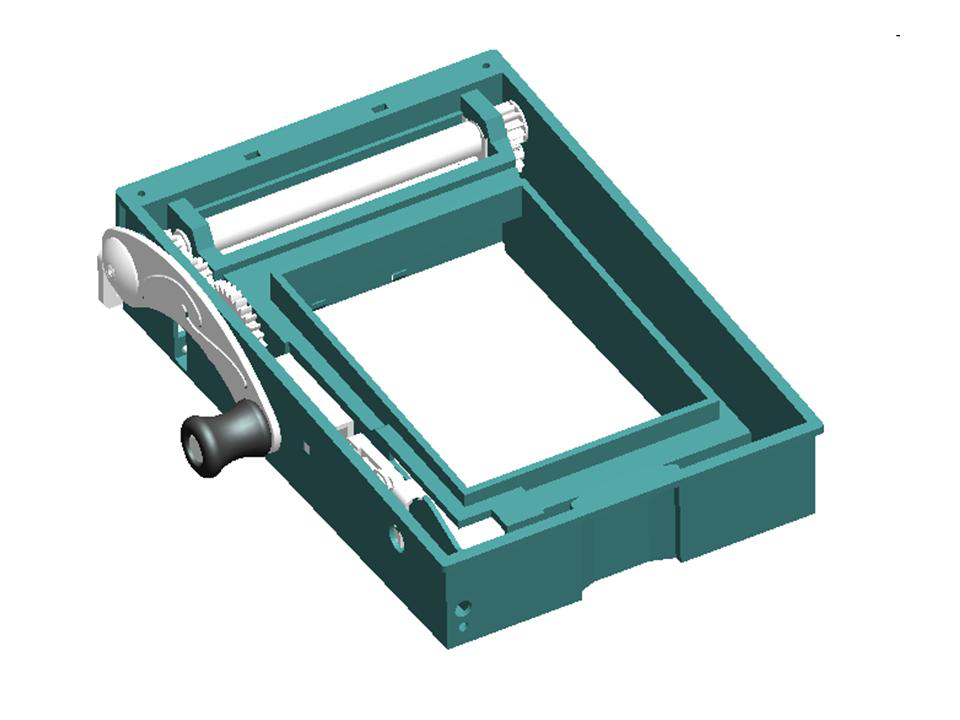
Пластмасови части на механизма
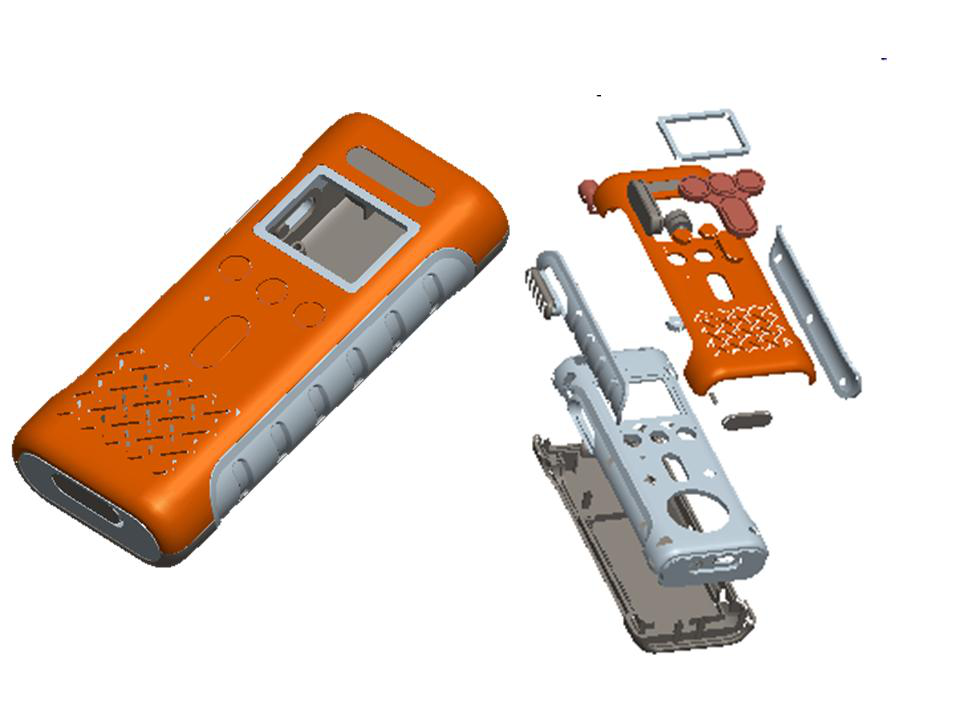
Пластмасови кутии за електронни
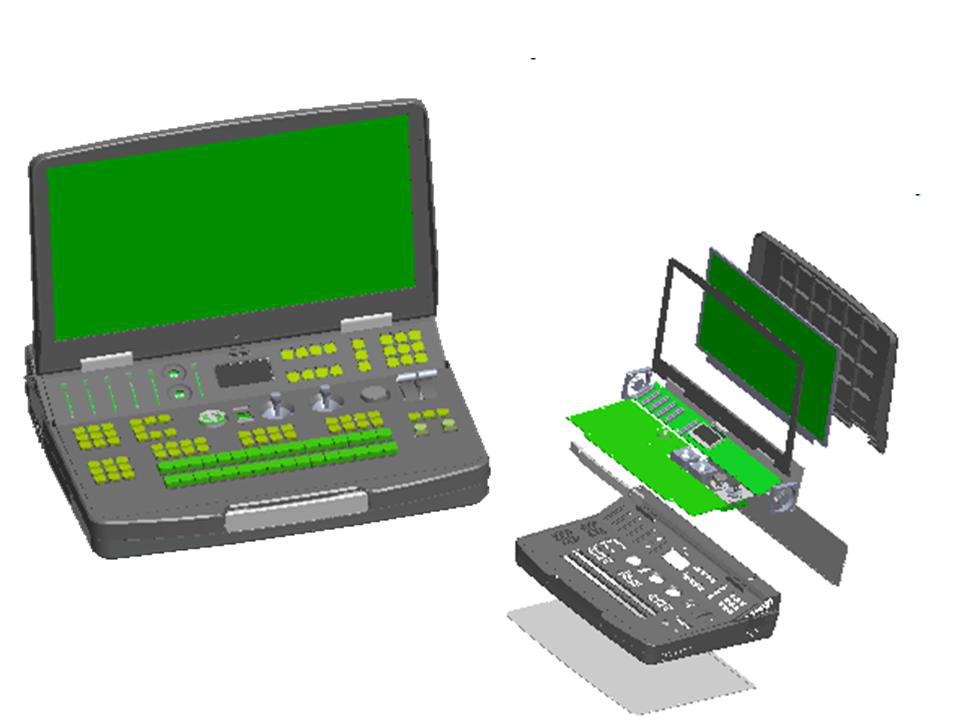
Пластмасов корпус за инструмент
По-долу споделяме подробности как да проектираме пластмасови части в три аспекта
* 10 съвета за проектиране на пластмасови части, които трябва да знаете
1. Определете външния вид и размера на продукта.
Това е първата стъпка в целия процес на проектиране. Според проучванията на пазара и изискванията на клиентите, определете външния вид и функцията на продуктите и формулирайте задачите за разработване на продукти.
Съгласно задачата за разработка, екипът за разработки извършва технически и технологичен анализ на осъществимостта на продукта и изгражда 3D модела на външния вид на продукта. След това, според реализацията на функцията и сглобяването на продукта, се планират възможни части.
2. Отделете отделни части от чертежите на продукта, изберете пластмасова смола за пластмасови части
Тази стъпка е да отделите частите от 3D модела, получен в предишната стъпка, и да ги проектирате като индивидуални. Според функционалните изисквания на частите, изберете подходящи пластмасови суровини или хардуерни материали. Например, ABS обикновено се използва в
черупка, ABS / BC или PC се изисква да има определени механични свойства, прозрачни части като абажур, фонарен стълб PMMA или PC, зъбни колела или износващи се части POM или найлон.
След като изберете материала на частите, може да се започне детайлният дизайн.
3. Определете ъглите на тягата
Наклонените ъгли позволяват отстраняването на пластмасата от матрицата. Без ъгли на тягата, детайлът би осигурил значително съпротивление поради триене по време на отстраняването. Външните ъгли трябва да присъстват от вътрешната и външната страна на детайла. Колкото по-дълбока е детайлът, толкова по-голям е ъгълът на газене. Едно просто правило е да имате 1 градусов ъгъл на газене на инч. Липсата на достатъчно ъгъл на теглене може да доведе до ожулвания по страните на детайла и / или големи маркировки на щифта на изхвъргача (повече за това по-късно).
Ъгли на газене на външната повърхност: Колкото по-дълбока е частта, толкова по-голям е ъгълът на газене. Едно просто правило е да имате 1 градусов ъгъл на газене на инч. Липсата на достатъчно ъгъл на теглене може да доведе до ожулвания по страните на детайла и / или големи маркировки на щифта на изхвъргача (повече за това по-късно).
Обикновено, за да изглежда добре повърхността, текстурата се прави върху повърхността на частите. Стената с текстура е груба, триенето е голямо и не е лесно да се отстрани от кухината, така че изисква по-голям ъгъл на изтегляне. Колкото по-груба е текстурата, толкова по-голям ъгъл на чертане е необходим.
4. Определете дебелината на стената / равномерната дебелина
Формоването с твърда форма не е желателно при шприцоване по следните причини:
1). Времето за охлаждане е пропорционално на квадрата на дебелината на стената. Дългото време за охлаждане на твърдо вещество ще победи икономиката на масовото производство. (лош проводник на топлина)
2) .По-дебелата секция се свива повече от по-тънката секция, като по този начин се въвежда диференциално свиване, което води до деформация или марка на мивка и т.н. (характеристики на свиване на пластмасите и pvT характеристики)
Следователно имаме основно правило за дизайн на пластмасови части; доколкото е възможно дебелината на стената трябва да бъде еднаква или постоянна през цялата част. Тази дебелина на стената се нарича номинална дебелина на стената.
Ако в детайла има някакъв плътен участък, той трябва да бъде направен кух чрез въвеждане на сърцевина. Това трябва да осигури еднаква дебелина на стената около сърцевината.
3) .Какви са съображенията за вземане на решение за дебелина на стената?
Трябва да е достатъчно дебел и твърд за работата. Дебелината на стената може да бъде от 0,5 до 5 мм.
Той също трябва да е достатъчно тънък, за да се охлади по-бързо, което води до по-ниско тегло и по-висока производителност.
Всяка промяна в дебелината на стената трябва да бъде възможно най-малка.
Пластмасова част с различна дебелина на стената ще има различни скорости на охлаждане и различно свиване. В такъв случай постигането на близка толерантност става много трудно и в пъти невъзможно. Когато варирането на дебелината на стената е от съществено значение, преходът между двете трябва да бъде постепенен.
5. Дизайн на връзката между частите
Обикновено трябва да свържем две черупки заедно. За оформяне на затворена стая между тях за поставяне на вътрешните компоненти (сглобка или механизъм на печатни платки).
Обичайните видове връзка:
1). Закрепващи куки:
Връзката с куки се използва често при малки и средни продукти. Характеристиката му е, че куките за закрепване обикновено са поставени на ръба на частите и размерът на продукта може да бъде намален. Когато е сглобен, той се затваря директно, без да се използват каквито и да е инструменти като отвертка, матрица за ултразвуково заваряване и други. Недостатъкът е, че щракващите куки могат да причинят по-сложна плесен. Плъзгащият механизъм и механизмът за повдигане са необходими, за да се осъществи връзката на куките и да се увеличат разходите за матрицата.
2). Винтови съединения:
Винтовите съединения са здрави и надеждни. По-специално, фиксирането на винт + гайка е много надеждно и издръжливо, позволяващо множество разглобявания без пукнатини. Винтовата връзка е подходяща за продукти с голяма заключваща сила и многократно демонтиране. Недостатъкът е, че винтовата колона заема повече място.
3). Монтажни шефове:
Връзката за монтиране на шефове е да се фиксират две части чрез плътната координация между каналите и дупките. Този начин на свързване не е достатъчно силен, за да позволи разглобяване на продукти. Недостатъкът е, че заключващата якост ще намалее с увеличаване на времето за разглобяване.
4). Ултразвуково заваряване:
Ултразвуковото заваряване е чрез поставяне на двете части в ултразвуковата форма и сливане на контактната повърхност под действието на ултразвукова машина за заваряване. Размерът на продукта може да бъде по-малък, инжекционната форма е сравнително проста и връзката е стабилна. Недостатъкът е използването на ултразвукова плесен и ултразвукова машина за заваряване, размерът на продукта не може да бъде твърде голям. След демонтирането ултразвуковите части не могат да се използват отново.
6. Подрязвания
Подрязванията са елементи, които пречат на отстраняването на която и да е половината от матрицата. Подрязването може да се появи почти навсякъде в дизайна. Те са също толкова неприемливи, ако не и по-лоши от липсата на ъгъл на газене от детайла. Някои подбивания обаче са необходими и / или неизбежни. В тези случаи е необходимо
подрязванията се получават чрез плъзгане / движещи се части в матрицата.
Имайте предвид, че създаването на подрязвания е по-скъпо при производството на матрицата и трябва да бъде сведено до минимум.
7. Подкрепете ребра / накрайници
Ребрата в пластмасова част подобряват твърдостта (връзката между товара и деформацията на частта) на детайла и увеличават твърдостта. Той също така подобрява способността за плесен, тъй като те ускоряват потока на стопилката по посока на реброто.
Ребрата се поставят по посока на максимално напрежение и деформация върху повърхностите на детайла, които не изглеждат. Пълненето, свиването и изтласкването на плесени също трябва да повлияе на решенията за поставяне на ребра.
Ребрата, които не се съединяват с вертикална стена, не трябва да завършват рязко. Постепенният преход към номиналната стена трябва да намали риска от концентрация на стрес.
Ребро - размери
Ребрата трябва да имат следните размери.
Дебелината на ребрата трябва да бъде между 0,5 до 0,6 пъти номиналната дебелина на стената, за да се избегне маркировката на мивката.
Височината на ребрата трябва да бъде 2,5 до 3 пъти номиналната дебелина на стената.
Реброто трябва да има ъгъл на газене от 0,5 до 1,5 градуса, за да улесни изхвърлянето.
Основата на ребрата трябва да има радиус 0,25 до 0,4 пъти номиналната дебелина на стената.
Разстоянието между две ребра трябва да бъде 2-3 пъти (или повече) номинална дебелина на стената.
8. Радиусирани ръбове
Когато две повърхности се срещнат, той образува ъгъл. В ъгъла дебелината на стената се увеличава до 1,4 пъти номиналната дебелина на стената. Това води до диференциално свиване и формовано напрежение и по-дълго време за охлаждане. Следователно рискът от повреда в обслужването се увеличава при остри ъгли.
За да се реши този проблем, ъглите трябва да се изгладят с радиус. Радиусът трябва да се осигурява както отвън, така и отвътре. Никога нямайте вътрешен остър ъгъл, тъй като той насърчава пукнатини. Радиусът трябва да бъде такъв, че да потвърждава правилото за постоянна дебелина на стената. За предпочитане е да има радиус от 0,6 до 0,75 пъти дебелината на стената в ъглите. Никога нямайте вътрешен остър ъгъл, тъй като той насърчава пукнатини.
9. Винтов шеф дизайн
Винаги използваме винтове, за да закрепим две половин кутии заедно, или да закрепим PCBA или други компоненти върху пластмасовите части. Така че винтовите шефове са конструкцията за завинтване и фиксирани части.
Болтът на винта е с цилиндрична форма. Шефът може да бъде свързан в основата с майчината част или може да бъде свързан отстрани. Свързването отстрани може да доведе до дебел пласт пластмаса, което не е желателно, тъй като може да причини следа от мивка и да увеличи времето за охлаждане. Този проблем може да бъде решен чрез свързване на шефа през ребро към страничната стена, както е показано на скицата. Шефът може да се направи твърд, като се осигурят контрфорсни ребра.
Винтът се използва върху шефа за закрепване на друга част. Има винтове за оформяне на резби и винтове за рязане на протектора. Винтовете за формоване на резби се използват за термопластични материали, а винтовете за рязане на резби се използват за нееластични термореактивни пластмасови части.
Винтовете за формоване на резби произвеждат женски резби по вътрешната стена на вдлъбнатината чрез студен поток - пластмасата се деформира локално, а не се нарязва.
Болтовете на винтовете трябва да имат правилни размери, за да издържат на силите на вкарване на винта и натоварването, поставено върху винта в експлоатация.
Размерът на отвора по отношение на винта е критичен за устойчивостта на отстраняване на резбата и издърпване на винта.
Външният диаметър на вдлъбнатината трябва да е достатъчно голям, за да издържи на напрежението на обръча поради образуването на резба.
Отворът има малко по-голям диаметър във вдлъбнатината за влизане за малка дължина. Това помага за намирането на винт преди забиване. Освен това намалява напреженията в отворения край на гнездото.
Производителите на полимери дават насоки за определяне на размера на вдлъбнатината за техните материали. Производителите на винтове също дават насоки за правилния размер на отвора на винта.
Трябва да се внимава да се осигурят здрави заваръчни съединения около отвора на винта в гнездото.
Трябва да се внимава да се избегне формован стрес при шефа, тъй като той може да се провали в агресивната среда.
Диаметърът на отвора трябва да е по-дълбок от дълбочината на резбата.
10. Повърхностна декорация
Понякога, за да имаме добър външен вид, често правим специална обработка на повърхността на пластмасовия корпус.
Като: текстура, високо гланц, боядисване със спрей, лазерно гравиране, горещо щамповане, галванично покритие и така нататък. Необходимо е да се вземе предвид при проектирането на продукта предварително, за да се избегне последващата обработка не може да бъде постигната или промени в размера, засягащи сглобяването на продукта.